Кольская ГМК делает ставку на «цифру» и умные технологии
В компании презентовали результаты промышленных испытаний оптимизационных моделей технологических процессов в одном из отделений цеха электролиза никеля.
Инновации – путь к эффективности
Кольская ГМК всерьез занялась цифровизацией производства. Сегодня это залог устойчивого развития компании. На предприятии идет непрерывный процесс совершенствования, улучшаются, модернизуются технологические процессы, реализуются проекты по программному обеспечению, внедряются цифровые инструменты. В настоящее время одно из главных мест приложения сил – цех электролиза никеля (ЦЭН) в Мончегорске.

По словам начальника цеха Константина Смирнова, переход на новую технологию производства никеля – методом электроэкстракции — потребовал инновационных решений практически на каждом производственном переделе. Начать же решили с отделения растворения и дегазации, которое стало пилотной площадкой для разработки оптимизационных моделей технологических процессов цеха.
— В качестве пилотного проекта определили этот передел, потому что он самый важный, определяет дальнейшую работу всех остальных участков. Насколько отработает отделение растворения и дегазации в части снятия драгметаллов, так и дальше пойдут все производственные процессы, — отметил Константин Смирнов. — Есть многие вещи, о которых стоит подумать: как это повлияет на передел гидрометаллургического отделения, какие реагенты будем использовать, в каком количестве и так далее. Поэтому, когда работа началась, коллеги из цеха активно включились в нее. Коллектив у нас молодой, набирался, можно сказать, с нуля, инженерно-технические работники росли вместе с этим переделом. Плюс поддержка технического управления, департамента инноваций. Первый результат, считаю, получился впечатляющим. Когда систему доделаем, она пройдет промышленные испытания, мы снимем очень много вопросов. Это и экономика, и безопасность.

Сами разработчики прогнозирующего алгоритма управления процессами растворения и фильтрации второго блока растворения в ЦЭН данный проект считают уникальным, так как он объединил в себе много центров компетенций, таких как вертикаль инноваций, производственный сектор, ремонтная служба, команда «Озера данных», разработчики BI-систем.
Модели для предсказаний
Разработка оптимизационных моделей технологических процессов цеха началась в сентябре 2022 года.
— В конце прошлого лета у нас возникла гипотеза относительно того, что в ЦЭН на переделе растворения и дегазации за счет применения оптимизационного алгоритма возможно снизить количество переходящих в раствор металлов платиновой группы, — рассказал руководитель департамента по инновациям и цифровым технологиям Кольской ГМК Дмитрий Санников. — Для этого мы провели диагностику передела, это оценка информационных данных, которые собираются из систем АСУТП, лабораторных информационных менеджмент-систем по качеству материалов продуктов и растворов. На основании этих данных мы посмотрели, возможно ли такое в теории. И только при подтверждении, что такие зависимости найдены, стали разрабатывать прототип алгоритма.

За три месяца команды разработчиков Кольской ГМК и главного офиса «Норникеля» разработали четыре оптимизационных модели. Две из них предсказывают, как меняется окислительно-восстановительный потенциал (ОВП) в реакторе с раствором никелевого порошка. Еще две модели спрогнозируют, что произойдет с цементной медью, необходимой для ведения технологического процесса растворения никеля в определенном диапазоне.
— Прогнозы идут каждые 10 минут. А до настоящего времени приходилось каждые три часа делать отбор пробы, относить ее в химлабораторию на анализ. В итоге технолог на переделе получает результаты только спустя 3-5 часов. Оперативно получая данные, можно более эффективно вести технологический процесс. Это подтвердили и сами технологи во время проведения эксперимента в последних числах декабря. Им удалось стабилизировать процесс. Только после этого, когда удалось получить неплохие результаты по переделу, мы вместе с цехом, коллегами из технического управления, смогли разработать план дальнейших шагов по реализации проекта.
Отметим, что прогнозирующий алгоритм ОВП и виртуальный датчик меди разработаны и реализованы на базе платформы «Озеро данных». Это первый успешный опыт пилотирования прототипа машинного обучения на платформе в компании «Норникель».
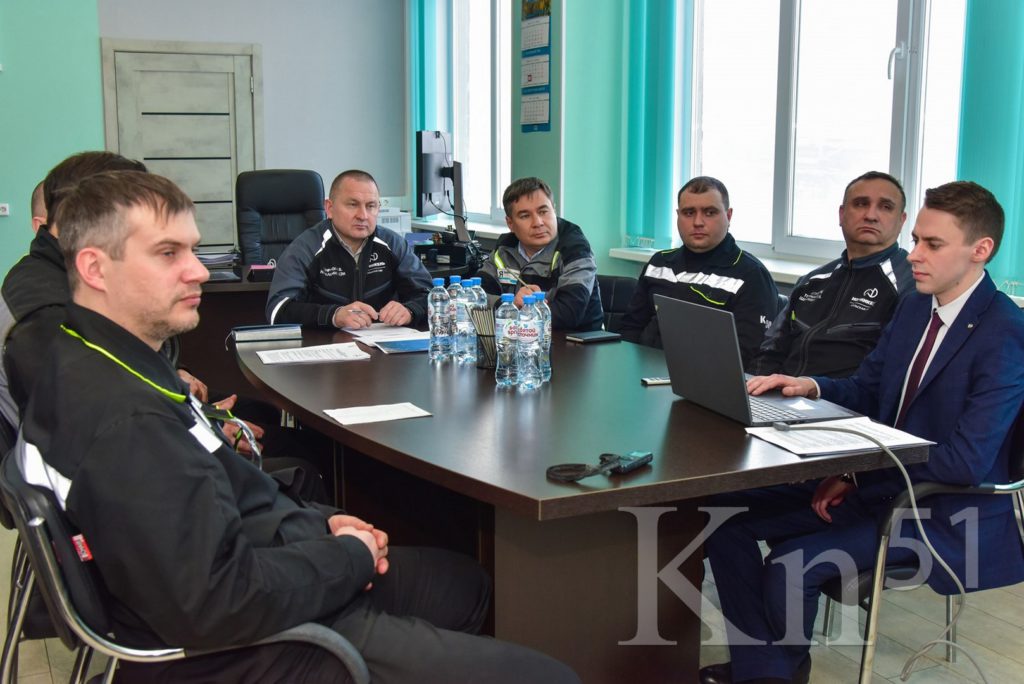
Ключевая цель – сквозная оптимизация
Дальнейший план реализации проекта включает в себя не только цифровые решения, но и работы по модернизации агрегатов передела хлорного растворения, исследовательскую работу, в том числе отбор дополнительных проб и оценку потенциала результативности.
— Сейчас перед нами стоит задача провести испытания по переводу второго блока передела хлорного растворения в автоматический режим управления, — рассказал Kn51.ru главный менеджер департамента по инновациям и цифровым технологиям Кольской ГМК Ярослав Крайнюченко. — Для этого необходимо разработать прототип автоматического управления дозированием никелевого порошка и цементной меди, разработать программу испытаний и подготовить участок к переходу в автоматический режим, а именно, вместе с ремонтными службами цеха сервисного обслуживания компании «Печенгастрой» и технологами ЦЭН провести ревизию шнековых дозаторов. Также совместно с центром автоматизации производства провести калибровку датчиков автоматической системы управления. И доработать нашу модель по прогнозированию окислительно-восстановительного потенциала и цементной меди в реакторах для работы в автоматическом режиме. Эти работы планируем завершить к концу июня 2023 года.
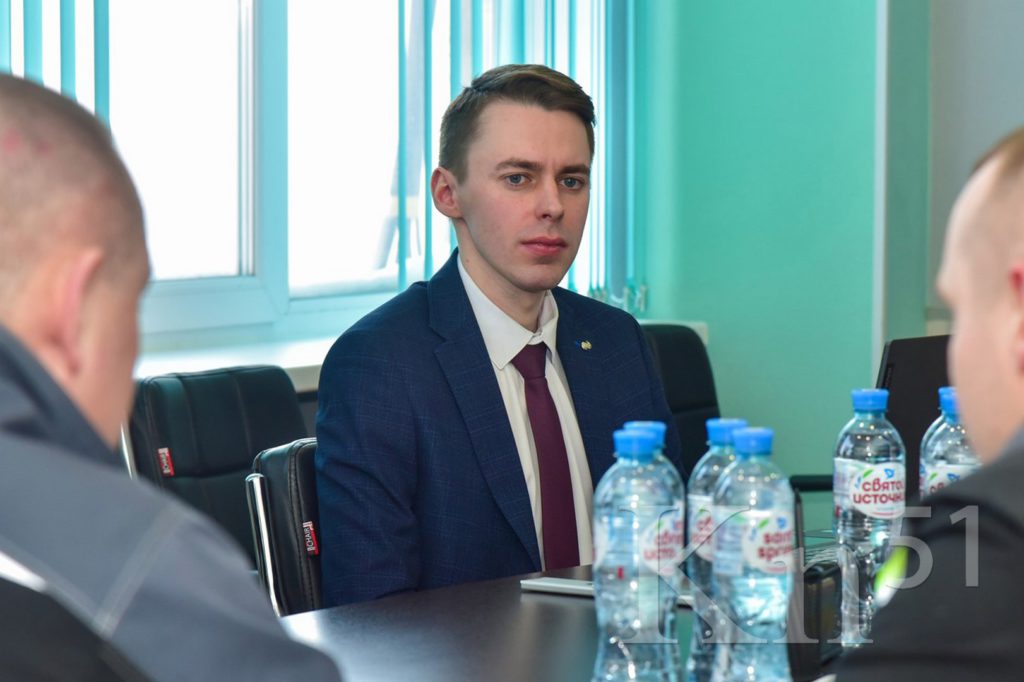
На презентации промышленных испытаний оптимизационных моделей не только подвели итоги работы по улучшению параметров производства в отделении растворения и дегазации, но и определили дальнейшие «цифровые шаги» в совершенствовании и модернизации технологических процессов цеха и Кольской ГМК.
— Напомню, наша ключевая цель – сквозная оптимизация технологических процессов Кольской ГМК, внутри дивизиона с нашими активами, которые находятся за пределами Мурманской области, и, конечно же, это сквозная оптимизация технологических процессов с Заполярным филиалом «Норникеля», для которого мы являемся поставщиком части оборотных материалов. Поэтому в чем более узких и стабильных границах мы будем поставлять коллегам обороты, тем эффективнее они смогут их перерабатывать. И тут уже мы становимся получателями, то есть потребителями их продукции – файнштейна.Первые работы в данном направлении мы проводим в рафинировочном цехе, цехе электролиза никеля, химико-металлургическом цехе, с коллегами из Харьявалты и Заполярного филиала «Норникеля» ведем проработку инфраструктурной части – готовим каналы передачи данных, верифицируем передаваемые данные, чтобы потом можно было разворачивать модели на междивизиональном уровне, — заключил Дмитрий Санников.

Игорь ПЕТРОВ. Фото Артема СЕНЧЕНКОВА
***
Мы всегда рядом! Следите за новостями в официальных группах Kn51 в соцсетях «ВКонтакте», «Одноклассники», «Дзен» и мессенджере «Телеграмм».